3D Printing Plastic
New 3D Printing plastic materials for fused deposition modeling (FDM) were created, validated and commercialized.
Problem
Common 3D printing filament is made from ABS or polycarbonate but one of the industry leaders wanted create new 3D printing plastic options. They hoped to expand their fused deposition modeling (FDM) offering to include new amorphous thermoplastics that had never been used before. Such products need to have good mechanical properties and very good processability (flow) combined with low shrinkage, so that the part does not warp when it cools.
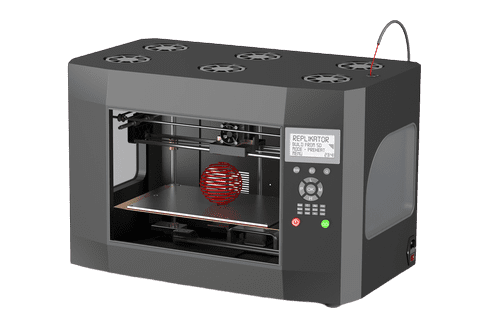
Action
We collaborated to identify the processing and mechanical properties of the incumbent plastics they already used. The client provided the 3D machine expertise whereas I brought the plastic materials knowledge. We then identified new thermoplastics with similar flow and mechanicals but with enhanced performance. We made the special high tolerance 3D printing plastic filament required by the machine.
Solution
The filaments of the two new materials, transparent ABS and ASA, worked perfectly on the existing machine without any significant changes. Parts were made where the transparent ABS offered high colorability plus, of course, transparency and the ASA offered extremely high UV resistance for outdoor use. That was all around 2004, way before 3D printing took off. Both materials were subsequently commercialized. Phantom Plastics is now developing new selective laser sintering (SLS) plastic materials that surpass the performance of existing materials.
See more about FDM material options on the Stratasys website. More Phantom innovations can be viewed on the Publications & Presentations page as well as the New Products Created page.