Composite Density Calculator
Introduction
There are many cases where a formulator needs to hit a certain density target. For example, a company asked me to make them a golf grip formulation using fillers to increase the density to a value they specified. Most people mistakenly believe that it is possible to calculate the density of a composite by taking the weighted mean of the densities of the polymer and filler, but that method doesn’t work, i.e. it gives the wrong answer. A graph of composite density versus weight % filler is a curve (see diagram below), not a straight line, so an equation is needed in order to calculate the correct density. For convenience, this page contains a composite density calculator to help you in your formulation design work.
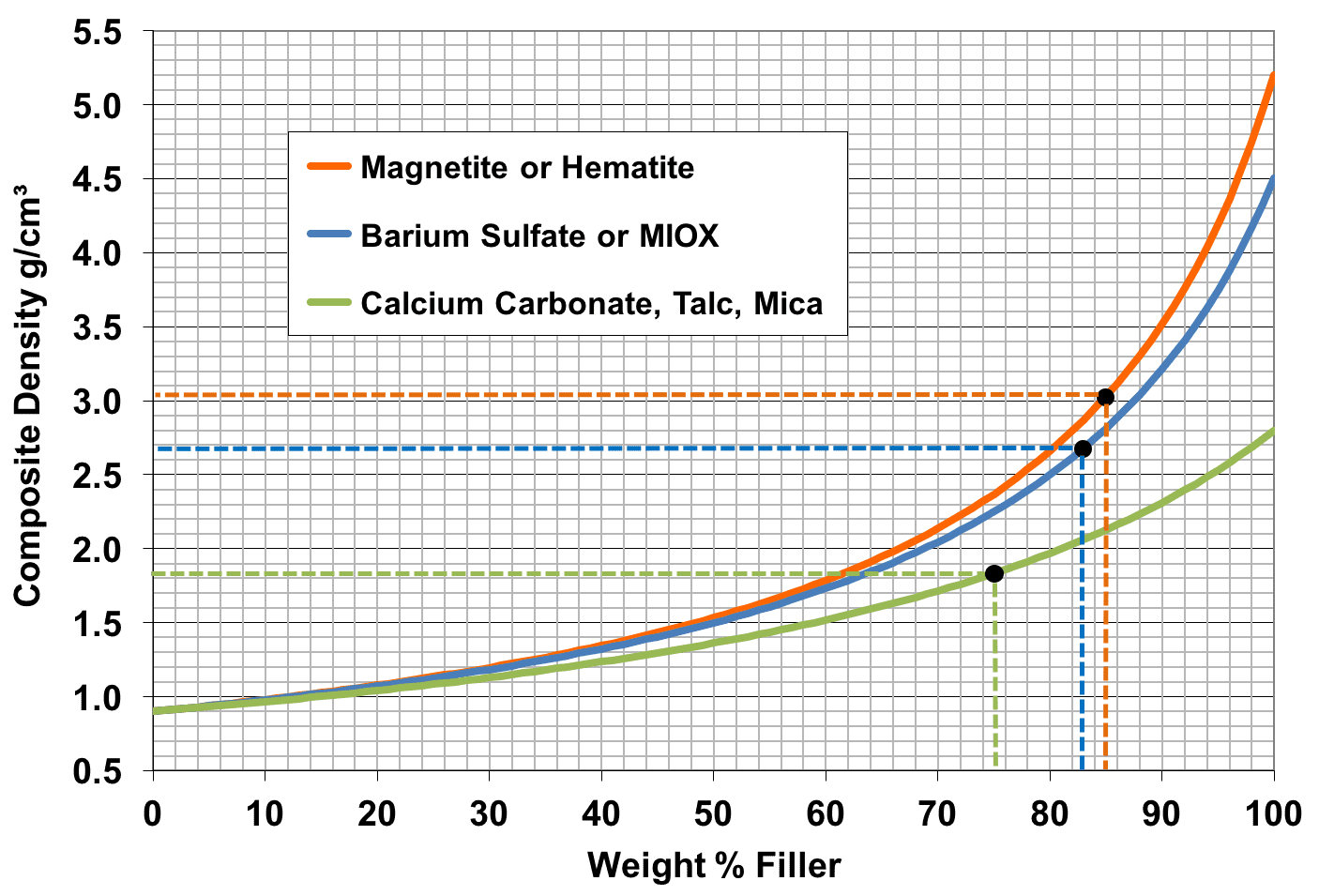
As an example, take 50 weight % filler with a density of 3 and 50 weight % of polymer with a density of 1 g/ml. You would expect the density of the composite to be (3+1)/2 which comes out to 2 g/ml. The actual density of that composite is 1.5 g/ml. What went wrong? The density of composites depend on the volume % of filler and not the weight percentage. Interestingly, all of the other properties like strength, stiffness and so on all depend on the volume percentage of filler as well – more about that on this page.
The Calculator
Here is the tool allowing you to instantly see the density of any polymer and filler combination. Just select your plastic and filler from the drop-down menus, then click elsewhere on the page to see the result instantly. Find out more about the different functional fillers on this page. If you have requests for materials to add then please contact us.
The Importance of Density Calculation
As mentioned, in some applications, one wishes to achieve a set target density. Rather than making several compounds and hoping to get lucky, by pre-calculating the density, you can save time and money.
Sometimes, once the composite is made, the measured density turns out to be different than the calculated density and that information can be valuable because it gives clues about possible problems. If the measured density does not match the predicted density, then the first thing to check is that the filler was actually dosed at the correct level. The way to tell that is usually to perform an ashing test whereby the plastic is burnt away leaving behind the inorganic filler which is more thermally stable than the polymer. One should make certain that the filler really does remain stable and does not lose mass during the ashing step. For example, some carbonates partially decompose, giving off carbon dioxide and thus losing mass when heated above a certain temperature. If ashing shows that the filler loading is indeed correct, then other phenomena may account for the unexpected measured density result.
If the actual composite has a density lower than predicted, then there may be air trapped in the material, perhaps because the filler was not properly wetted out. This can be remedied by changing the compounding parameters or by using a wetting aid / surfactant.
If the measured density is higher than the calculated theoretical density, then the filler may have nucleated crystal formation in the polymer matrix. Crystals have higher density than the amorphous phase, so if the addition of particles nucleates crystal formation, then an increase in the amount of crystalline phase can alter, i.e. increase the density of the polymer and therefore the composite. Such effects tend to be small because the crystalline phase has marginally higher density than the amorphous phase.
Credits
I have been very lucky to have the support of AnnaLytix, experts in data analysis, to put together an online calculator. The online composite density calculation tool includes preset values for most plastics and fillers, so you don’t have to look them up. I hope you find it useful and I thank AnnaLytix for making this dream of mine come true
See AnnaLytix.com for information on their business intelligence and data analytics services.