Glossy Piano Black Plastic
Problem
One of the largest, most admired companies in the World called with a problem. They were having trouble with a certain glossy piano black plastic part. They needed it to have a so-called “piano black” surface finish and at the same time meet stringent mechanical requirements and meet extreme tolerances when machined into the final shape. They could get either the appearance or the other properties but not both.
Having tried everything they could think of and being under extreme time pressure, they asked whether Phantom could come up with a solution. The problem sounded particularly challenging, especially as I knew how clever the people who had tried to solve it were. I asked for more details, so that I could start looking for a solution.
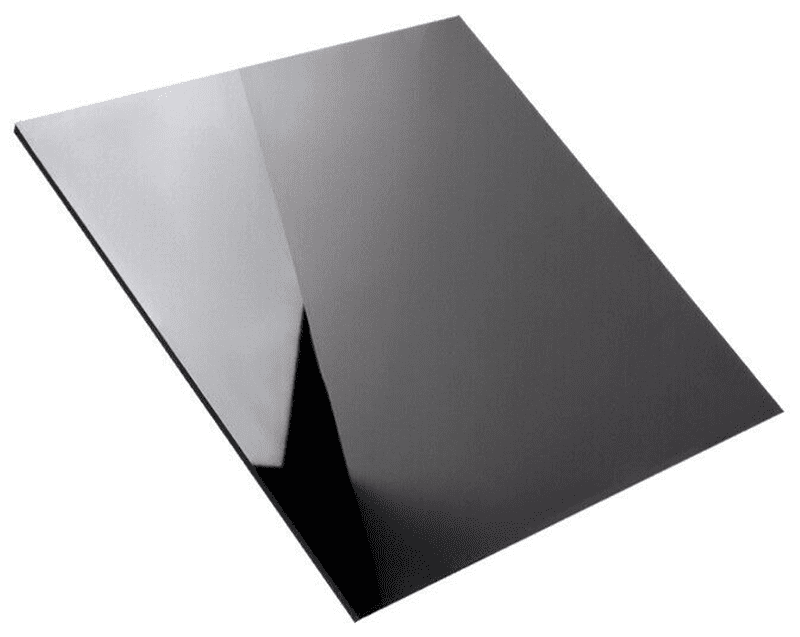
Action
The company was an OEM and they wanted me to work with their supplier of high performance plastics to create a new formulation that could meet all of the requirements. First my client wanted an NDA, then once that was signed, we would need a second NDA between Phantom and their supplier. Rather than wait for the paperwork to be completed, I jumped in right away and started researching options. Within a few hours I had the answer and told the client that I was ready. They insisted that we get all of the paperwork signed before I told them anything. It took about two weeks for the papers to be signed by all three parties, which is very fast for such large organizations.
Solution
We had a meeting in which I showed what the solution was and explained how it worked. Piano black is the name given to an ultra-high gloss black surface. In the case of pianos or automobiles, the effect is obtained by applying a high gloss lacquer on top of a painted black surface. The same approach can be used in plastics but that is rather expensive, often too expensive to justify. In order to simulate a clear lacquer layer, a black transparent plastic is used. The problem is that additives such as fillers, lubricants or pigments put into the formulation tend to scatter light, ruining the transparency and resulting in a milky grey, dull appearance. Thus, the secret was to identify additives that would perform their function while remaining invisible within the plastic.
The special formulation required an additive with the right optical properties, the right particle size and dispersion level and low enough hardness to make machining go smoothly without undue wear and maintenance. At last they knew how to make their glossy piano black plastic without sacrificing either appearance or performance.
When working with large multi-nationals, this is not the first time when Phantom had the answer in hours or days but it took months for them to get the paperwork in place. That’s another reason to work with smaller, more nimble consultancy firms – it is often much quicker than proceeding internally. Many case studies of problems solved can be found in the dropdown menu on the homepage. Even if you don’t see your exact problem listed there, give Phantom a call anyway and I’ll tell you whether I can help.