Biodegradable Polymer
Problem
I accepted a one year post-doc position in Sweden to make biodegradable polymers. The research group there had been making polymers based on the same chemistry for several years. They cranked out many publications but in my opinion, that topic had been explored enough. I didn’t want to repeat the same work over and over again.
The goal was to make a biodegradable polymer for controlled release drug delivery within the human body. However, l could see no evidence that the polymers they synthesized were actually safe or that they decomposed to safe products. I decided to invent something truly new and, of course, safe.
Action
The first step was to get up to speed because my prior work had all been on electrically conductive polymers. I read around a hundred papers on biodegradable polymers to see what the current state of research was.It quickly became clear that researchers were making several different types of polymer in order to be able to tailor their degradation rate. Polyethers, polyesters and polycarbonates were being made and to me that strategy seemed wasteful.
I researched to check the state of the art and then designed my own strategy. I started by obtaining a list of additives approved for use in food because those are proven to be safe for human consumption and of course they are widely available at a reasonable price.
I got the list from the pharmacy and scoured the hundreds of chemical food additives to see whether I could react any of them together to form a new type of biodegradable polymer. I found two additives that could be used, so I was ready to get started on synthesis. I needed to be fast, because the post-doctoral position was for just one year and that is not much time to conceive, synthesize and characterize a new polymer.
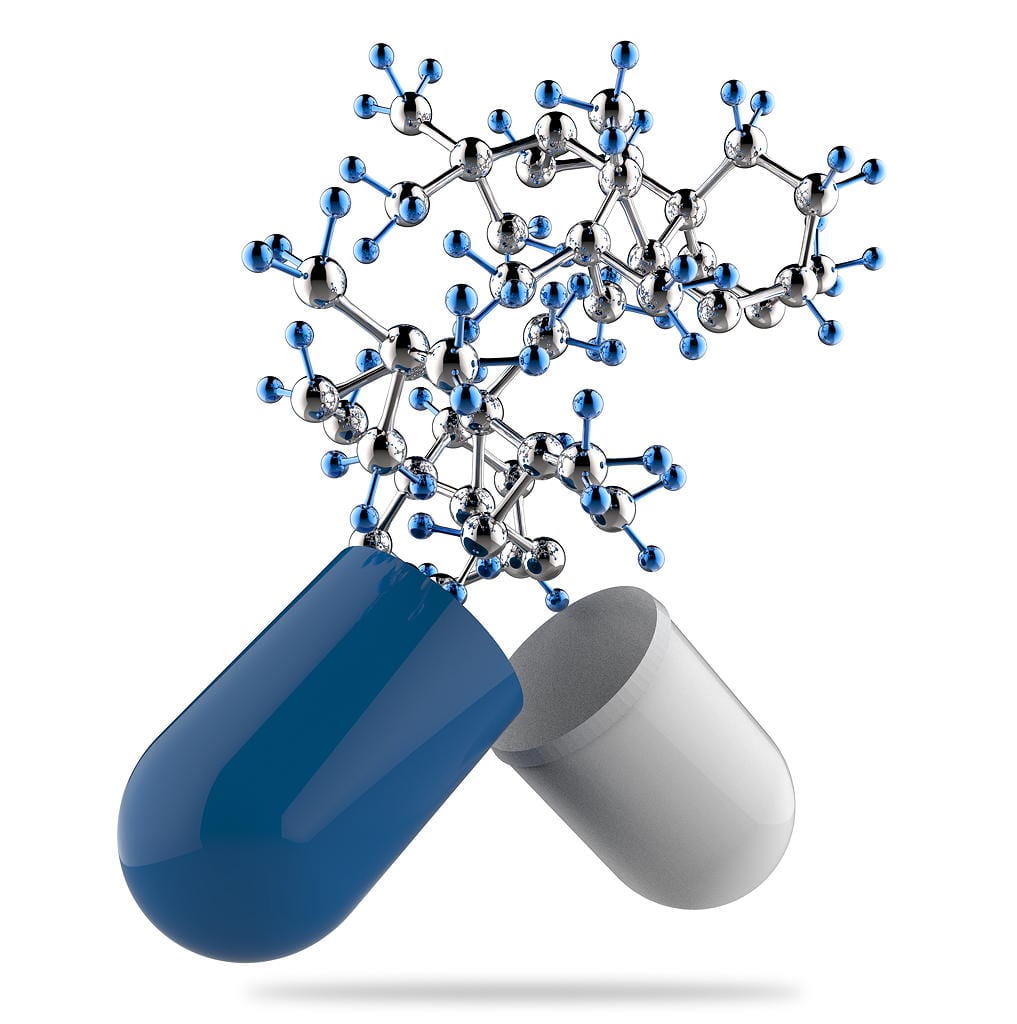
Solution
By reacting EDTA dianhydride and hydroxy-terminated PEG together, I was able to make a totally new range of PEG-based polymeric ionomers. Upon degradation, such a polymer would biodegrade back into those same safe monomers used to make them.
This new polymeric ionomer gel had another great advantage over other types of biodegradable polymers. Each ester link on the polymer backbone had an adjacent carboxylic acid moiety formed when the anhydride had reacted with the hydroxyl group on the PEG chain end.
As any chemist will know, acids catalyze the hydrolysis of ester groups, so the polymer degradation of the new degradable ionomer would be accelerated compared to a normal polyester. This would give a medium rate of degradation.
If the carboxyl groups were neutralized with a weak base, then the catalytic degradation effect would be switched off because the acidity would be removed and so the polymer would degrade more slowly.
On the other hand, when the carboxylic acids were neutralized with a strong base like sodium or potassium, the result would be an alkaline group next to the ester linkages, which leads to more rapid base-catalyzed hydrolysis, so a fast degradation rate.
This breakthrough meant that for the first time it was possible to make just one polymer and then decide how fast it would degrade just by selecting the pH of the counterion. Furthermore, use of copper, silver or zinc as a counterion would provide additional antibacterial performance to protect the patient from infection.
Later innovations can be found on this website and on the New Products Created page.