Halloysite Clay Nanotubes
Introduction to Halloysite Filler
Halloysite filler is a natural nano clay with identical chemistry to the more common kaolinite clay. There has been a huge amount of hype around this product but actual commercial applications have been very slow to develop. The performance is not sufficient to justify the price, or in many instances, the results shown in academic articles cannot be replicated in an industrial setting. Nevertheless, several commercial sources of halloysite exist, so that may drive down price over time.
While synthetic nanotubes have been the subject of much attention, they have proven expensive to manufacture. The idea of a natural nanotube has great appeal to the scientific community but also to industry. It would seem clear that a nanotube, with a price similar to kaolin, would be a hit. The tubes vary depending on the deposit from which they come. By far the most well-known is Imerys’ New Zealand deposit. Imerys is a world-leading producer of minerals and they have sold high purity halloysite, mainly for fine china and porcelain, for many years. Many other deposits have been reported all around the world. During my tenure as CTO of a halloysite company, I counted around 50 deposits, of which perhaps five or so seemed potentially viable. I collected and read over 700 articles and patents on halloysite to become the leading expert on the subject. Some of that information will be outlined here.
Halloysite Filler Material Properties
In order to understand what halloysite can do, one must first understand the intrinsic properties of the material. Once those are identified, commercial applications become immediately apparent. An excellent overview of the nomenclature [1,2] and characterization of halloysite has been given by Churchman and Carr [3]. Other excellent overview texts exist [4,5].
Chemical formula: Al2Si2O5(OH)4 . nH2O
CAS Number: 1332-58-7
RMM: 294.19
Density: 2.54 gcm-3
Mohs hardness: 2.5
Colour: White
Refractive index: 1.534 (birefringence 0.002)
Melting point: >1300°C / >2400°F
CTE: 10 x 10-6 K-1 ⟂ to TUBE, 6 x 10-6 ∥ to tube
Thermal conductivity: 0.092 Wm-1K1
Specific heat capacity: 0.92 kJkg-1K-1 2.3 kJL-1K-1
Dielectric constant: 10 – 15
Solubility: Insoluble in water, acids, bases & solvents
Reactivity: Unreactive (except to strong acids and bases)
1. The nomenclature of the Halloysite minerals, D. M. C. MacEwan, Mineral., Mag., 28: 36-44 (1947).
2. G. T. Faust, The endellite-halloysite nomenclature, Amer. Mineral., 40: 1110-1118 (1955).
3. The Definition and Nomenclature of Halloysites, G. J: Churchman and R. M. Carr, Clays and Clay Minerals, 23: 38-388, (1975).
4. Halloysite clay minerals: a review, E. Joussein, S. Petit, J. Churchman, B. Theng, D. Righi, and B. Delvaux, Clay Minerals, 40: 383-426 (2005).
5. Clay Mineralogy – 2nd Edition, R. E. Grim, McGraw-Hill, New York, USA (1968).
Morphology and Materials Properties of Halloysite Filler
The tubular, high aspect ratio particles are ~1-2 microns long, ~50nm across and with a ~15 nm hole or “lumen” (Figure 1). The surface area of halloysite depends on processing and can be selected in the range ~ 50-150 m2 g-1. The measured modulus is ~150 GPa [7,8], compared to the calculated value of ~ 200-300 GPa [9]. The tubes can flex almost 90 degrees without breaking7 and have a dry crush strength [10] of >1500 GNm-2), >250 000 psi or >130 tons per square inch (beyond the limit of the machine used).

Figure 1 Scanning electron micrograph of pure, as-mined, halloysite
6. Direct Measurements of the Young’s Modulus of a Single Halloysite Nanotube Using a Transmission
7. Electron Microscope with a Bending Stage, Dong Lu, Haibin Chen, Jingshen Wu and Chi Ming Chan, Journal of Nanoscience and Nanotechnology, 11: 7789–7793 (2011).
8. Elastic modulus of halloysite nanotubes, B. Lecouvet, J. Horion, C. D’Haese, C. Bailly and B. Nysten, Nanotechnology 24 (10): 1-8 (2013).
9. Structural, Electronic, and Mechanical Properties of Single-Walled Halloysite Nanotube Models, L. Guimãres, A. N. Enyashin, G. Seifert, and H. A. Duarte, J. Phys. Chem. C, 114 (26): 11358–11363 (2010).
10. Study of the effect of compaction on the surface area and porosity of six powders by measurement of nitrogen sorption isotherms, S. J. Gregg and J. F. Langford, J. Chem. Soc., Faraday Trans. 1 ,73, 747-759 (1977).
The formation mechanism was the subject of intense debate for decades. Now it is generally accepted that halloysite can form from kaolinite, feldspar, rhyolite or ferruginous chlorite under the influence of hydrothermal action or weathering in nature.
Chemistry and Surface Chemistry of Halloysite
In terms of chemistry, halloysite is the same as kaolinite except that the sheets are rolled into tubes. The asymmetrical sheets, when rolled up, give the outside of the tube a silica-like chemistry and the inside an alumina-like chemistry (Figure 2). This has been confirmed by spectroscopic means. For example RAMAN and FTIR spectroscopy indicate the presence of Al-OH groups inside the lumen but no silanol (Si-OH) groups have been detected, indicating a low concentration. Such spectroscopic studies have been useful in several ways. It can be shown that certain small, polar molecules intercalate between the sheets (discussed in detail in the remediation section). Dehydroxylation of halloysite upon heating can also be followed and surface treatment can be confirmed by spectroscopic means.
- Aluminosilicate mineral: Al2Si2O5(OH)4 . nH2O
- Molecular weight: 294.19
- CAS: 1332-58-7
- Surface energy: 420-530 mJm-2
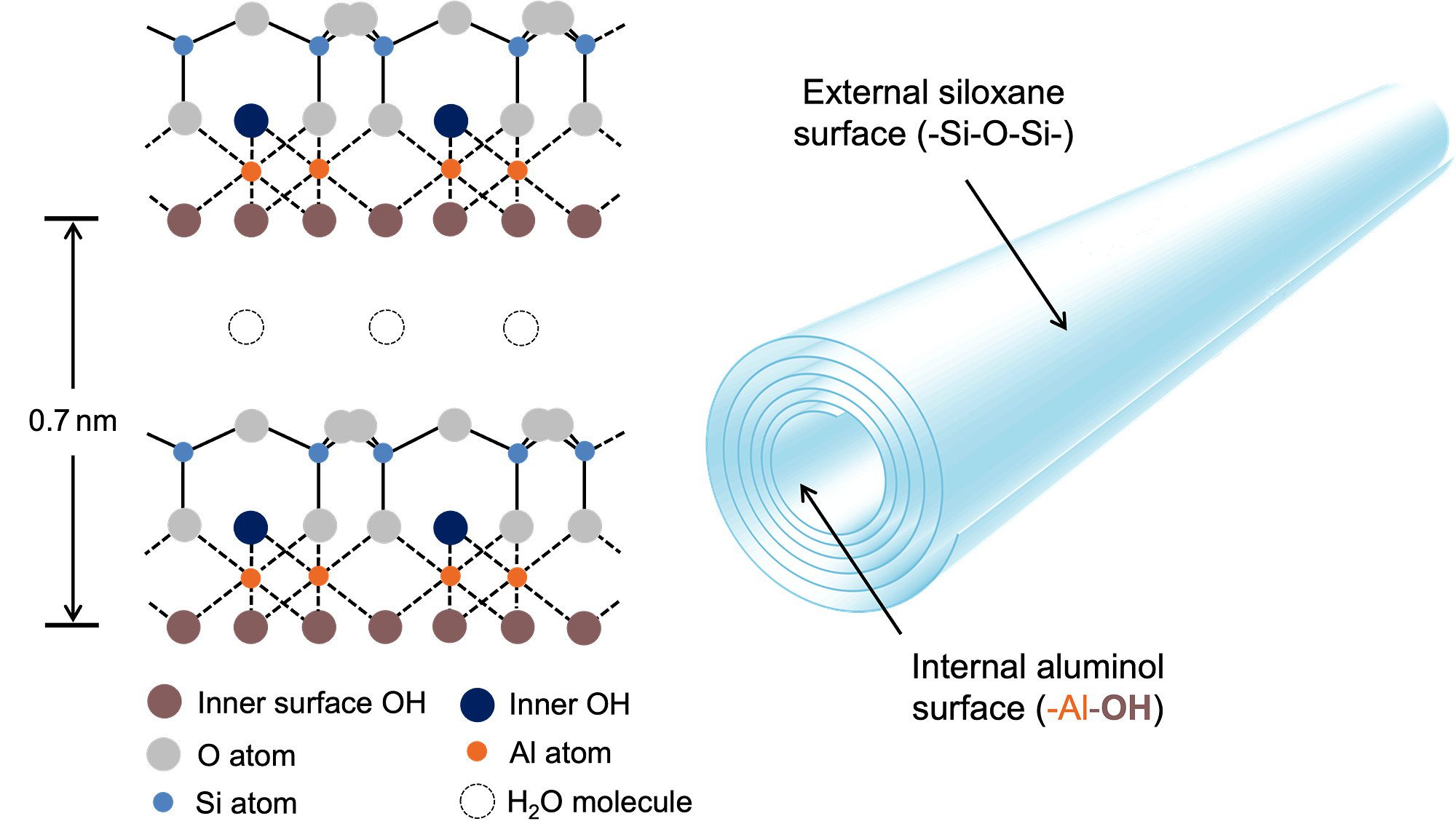
Figure 2 Structure and chemistry of halloysite nanotubes
One study used environmental TEM to keep the sample wet and to watch as the halloysite dehydrated to form the 7Å type. Interestingly and counter-intuitively, the diameter of the tubes was found to increase by approximately 10 percent as the water was lost in forming the 7Å material. Other workers reported a 60 percent expansion from 300 to 500nm tube diameter. This was attributed to an effect analogous to a scroll loosening as the water that held the layers tightly together is lost. Dehydration temperature was found to depend on humidity. At room temperature 10Å converts to 7Å at 30 percent humidity or below. At 40 percent humidity 40°C is required. At 100 percent humidity 65°C is needed and when submerged in water dehydration takes place at 95°C.
Once 7Å halloysite has formed, it cannot be rehydrated to form the 10Å variant. No rehydration occurred even after exposure to 100 % humidity for two months. This is in contrast to other clays such as Montmorillonite, which will rehydrate and swell when exposed to high humidity or water. However, the 10Å spacing of halloysite can be retained if the interlayer water is first exchanged for ethylene glycol.
[Interlayer H2O] (Surface H2O)
Halloysite 98% humidity Si2Al2O5(OH)4 [2.0] (0.6) H2O
Halloysite 55% humidity Si2Al2O5(OH)4 [2.0] (0.3) H2O
Halloysite dried at 250°C then held at 55% humidity Si2Al2O5(OH)4 [0] (0.3) H2O
pH in water 6.4-7.2
CEC Halloysite 7Å 11 meq/100g
Halloysite pH behavior related to mineral formation and stability has been studied. The effects of acid on halloysite were reported as early as 1925 and then again in 1943, the latter on both halloysite and calcined halloysite. More recently, White et al. showed that the tubular shape remains intact even after 84 days of exposure to 1M NaOH (pH 14) or 1M H2SO4 (pH 0) although slow etching does take place resulting in an enlarged lumen and correspondingly thinner walls. Acid etching can be accelerated using 3M H2SO4 and heating to 90°C which increases the pore volume and surface area to create a highly effective sorbent Acids remove the aluminium containing layers whereas alkali etches away the silica layers. Abdullayev et al. etched out the alumina inside the tube using sulfuric acid which increased the lumen volume considerably. Extraction of alumina from halloysite is particularly favorable compared to other clays with recovery of up to 100%.
The cation exchange capacity of 7Å halloysite is generally reported to be ~11 meq/100g and this can be increased to almost 50 meq/100g simply by soaking in sea water. For comparison, kaolinite has a CEC of 5 and that increases to just 8 meq/100g upon soaking in sea water. It has also been stated that the CEC for 7Å lies between 5-10 meq/100g compared to 40-50 meq/100g for the 10Å material.
All natural deposits contain different minerals. For example, kaolinite and halloysite occur together in many instances. It is vital to be able to distinguish between the two. For many years there was no reliable method to do so because the two minerals are so similar in chemistry and structure. The James Hutton Institute in Scotland (formerly known as the Macaulay Land Use Research Institute) are the leading experts in mineral characterization and identification. In particular with Dr. Stephen Hillier who is Chairman of the Clay Minerals Group and winner of the prestigious Reynolds Cup for identification of complex mineral mixtures. He employs an x-ray diffraction method, which is the only technique to unambiguously identify pure halloysite and mixtures of halloysite and kaolinite (Figure 3). This is supplemented with further methods including mercury porosimetry, XRF, ICP-MS, TEM, SEM and several other techniques that ensure the material is thoroughly characterized.
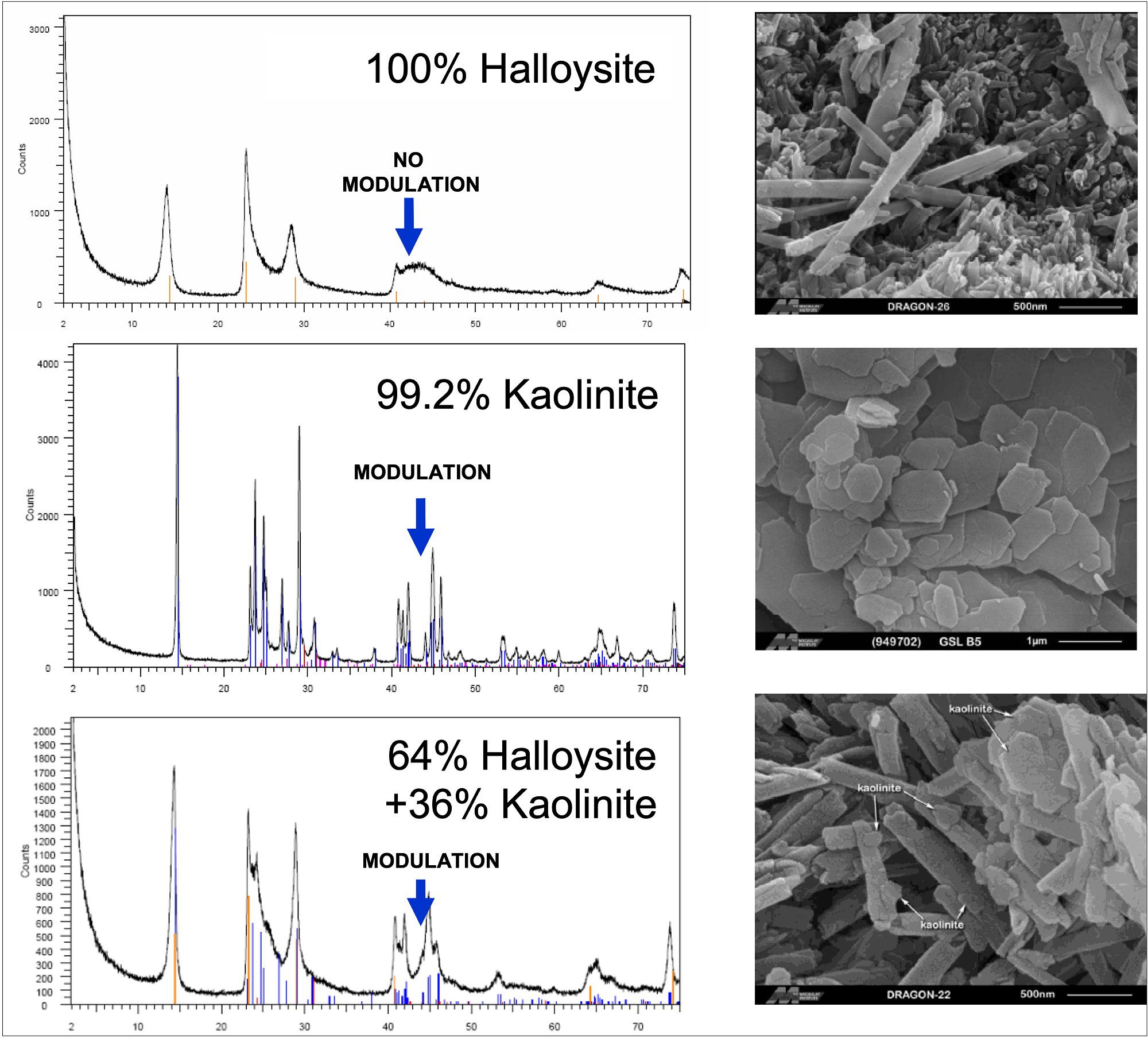
Figure 3 X-ray diffraction (XRD) to measure halloysite purity level
Density
Halloysite can occur in several shapes including spherical, sheet and the elongated tubular form, the latter is most prevalent and of most use due to its higher aspect ratio. The published density for halloysite varies over a range. One source lists 2.55 – 2.65 gcm-3 consistent with a calculated density of 2.59 gcm-3.
Density: 2.54 ± 0.03 gcm-3
The hollow shape means that halloysite has around 20 percent unfilled volume. This has an effect on the effective density of halloysite when it is encapsulated within a matrix. For example, if a composite is made in thermoplastic and the polymer fills the inside of the tube then the effective density of the halloysite is 2.54 gcm-3. However, if the inside of the tube is not filled by the polymer then the effective density of the halloysite is 20% less, i.e. ~ 2.00 gcm-3 because of the air trapped inside the lumen. It is even possible to determine whether the halloysite particles are unfilled, partially filled or completely filled by comparing the measured density of the prepared composite to the calculated theoretical density.
There are potential advantages to leaving the tubes unfilled. For example, this is gives thermal insulation, as found for hollow glass beads (see Thermal Properties section). Unlike glass beads though, halloysite also reinforces. Leaving the tubes unfilled also provides a reinforced composite of lower density, which is especially desirable for example in the automotive and aerospace industries.
Mineral hardness is normally measured on the Mohs scale with values ranging from 1 (softest) to 10 (hardest). The Mohs scale is far from linear so in some instances it is more appropriate to use another scale such as Knoop, Brinnel or Vickers Hardness. When it comes to the use of minerals as fillers in plastics, elastomers and coatings, the Mohs scale is particularly suitable because it relates to the ability of the mineral to scratch other materials. This means that it can give an indication as to whether the mineral can cause wear in processing equipment. Typical fillers have Mohs hardness between 1 (talc) and 3 (calcium carbonate). halloysite has Mohs hardness of 2.5 and there is therefore no concern over wear in extruders or other processing equipment.
Mohs Hardness: 2.5
Optical Properties of Halloysite
While spectroscopy can be used to characterize halloysite as mentioned above, the optical properties of the material itself indicate further commercial applications for the material. Halloysite in its pure form is a white solid which is ideal for incorporation into plastics, paints and coatings.
The refractive index of halloysite depends on the degree of hydration.
10Å form (fully hydrated) 1.522 ± 0.003
7Å form (partially dehydrated at room temperature) 1.534 ± 0.003
7Å form (dried at 100°C) 1.548 ± 0.003
Birefringence is reported as > 0.002
The birefringence (differing refractive index parallel and perpendicular to the long axis of the tube) is expected for particles of asymmetrical atomic structure. Non-linear optical properties have been reported as well.
It has proven possible to make transparent, colorless films of halloysite in LDPE (25 weight % loading) PLA (30 % loading), PVA (10% loading) and SBR (65 % loading).
UV Transparency of Halloysite
Unlike other minerals, halloysite is transparent to UV light. This was attributed in part to the very low iron content in pure halloysite compared to other minerals. In fact, one study used several clays as UV blockers for sunscreen and found that all clays tested were effective except for halloysite because it is UV transparent. As we shall see later, this UV transparency has already proven useful in commercial products.
Thermal Properties of Halloysite Clay
Surprisingly little work has been done to measure the thermal properties of halloysite. However, one very detailed paper does exist (see Mostav and Gaber below). The specific heat, thermal diffusivity and thermal conductivity were investigated between room temperature and 280°C. It was found that thermal conductivity and diffusivity both decreased sharply upon heating to 100°C due to water loss and from then onward maintained steady values shown below.
Specific heat capacity: 0.92 kJkg-1K-1 (0.22+0.008 cal g-1 deg-1)
Thermal conductivity: 0.092 WK-1m-1 (2.2 x 10-4 cal cm-1 sec-1 deg-1)
Thermal diffusivity: 5.04 x 10-4 cm2 sec-1
The specific heat capacity is identical to kaolinite over the temperature range 50 to 300K. The volumetric specific heat capacity for halloysite is 2.3 kJL-1K-1, i.e. the same as for other minerals, polymers and other solids. Note that the volume specific heat capacity (not weight) is the correct unit to use for mineral fillers.
Heating studies have determined that the tubular structure remains intact to very high temperatures in the range 900°C to 970°C.
Study of Thermal Properties of Endellite Clay Compound, M. S. Mostafa and A. Gaber, Journal of Thermal Analysis, 35: 2311-2321 (1989).
The thermal conductivity and diffusivities are very low, in the same range as for hollow glass beads used as an additive to improve thermal insulation. Halloysite could therefore be used in similar applications but with the added advantage of mechanical reinforcement, which is not the case when using hollow glass beads.
The initial weight loss is due to removal of surface moisture. Thereafter halloysite is thermally stable up to over 400°C, which means that it can and has been compounded into all types of polymer from up PE to PEEK.
The loss of water above 400°C makes halloysite a good reinforcing and halogen free flame retardant as the water released quenches the fire. More information on halloysite as a flame retardant in plastics and elastomers is given later.
It if often desirable to lower the coefficient of thermal expansion for ceramics, plastics, adhesives or coatings by incorporating a particulate reinforcement that has a low CTE. The CTE of halloysite has been measured for the temperature range 25-350ºC and found to be low compared to several other common minerals.
CTE of Halloysite
10.0 x 10-6 ± 1.5 perpendicular to the layer
6.0 x 10-6 ± 2.0 parallel to the layer
The low CTE and high aspect ratio of halloysite make it an effective additive to reduce the CTE of plastics. This has been demonstrated in epoxy resin.
The reduction in CTE and warpage is also applicable to other polymers. For example, this effect has been commercialized in HDPE where it gave significant advantages compared to other fillers tested.
Electrical Properties of Halloysite
Kaolinite is used as a filler in electrical applications due to its insulating properties. As halloysite is chemically analogous to kaolinite, it would be expected to be a good electrical insulator as well. Modeling predicts a high band gap indicative of a good electrical insulator. Measurement shows a low conductivity of just 3.5 x 10-5 Scm-1.
Although chemically speaking halloysite and kaolinite are identical, halloysite possesses additional water bound between the layers. These water molecules can move in an applied field, thus the dielectric constant is increased somewhat compared to kaolinite, which does not contain such bound water (see the Halloysite Handbook below for more specifics).
Heating halloysite leads to lower dielectric constant due to irreversible loss of water. Even heating to just 220ºC gives a marked improvement. It can be expected that heating to 400-600ºC, which drives off all bound water and dehydroxylates the mineral, will lead to very low dielectric constant values across the frequency spectrum.
Although halloysite is intrinsically a good electrical insulator, it can be made conductive. This has been accomplished by electroless coating with metal or by polymerizing a coating of conductive polymer such as polyaniline or polypyrrole onto the tube surface. Such anisotropic, conductive particles are in demand for applications including EMI shielding and z-axis adhesives. See also the section on electrically conductive halloysite.
Halloysite Applications
Fine china and porcelain
Halloysite has long been used and is a ideal because of high whiteness, which gives a translucent article once fired. The tubular shape helps prevent sag, although it can also increase shrinkage. Large amounts of halloysite are supplied into the Asian market from the New Zealand deposit.
Reinforcement for plastics
Minerals are well-known as fillers for plastics. Those with a high aspect ratio, i.e. ratio of length to width, are effective at increasing both stiffness and strength of the polymer. In terms of aspect ratio, halloysite is similar to, for example, standard talc or wollastonite and inferior to high aspect ratio talc, mica, or glass fibre. Quite simply, it cannot compete in cost or performance with those latter products. In a few instances, halloysite does give potentially viable reinforcement, particularly at very low loadings, around 1 weight% in nylon 6. That is believed to be a result of alteration in the crystallization behaviour of the nylon.
Nucleation of polymer crystallization
As mentioned above, halloysite can nucleate crystal growth in thermoplastics. In fact, it nucleates a very wide range of plastics including PE (very rare), PP, polyamides and some polyesters (PBT, PLA). Nucleating agents are big business so this effect could be commercially applicable assuming the halloysite can be competitive with incumbent solutions. There is a patent on nucleating polyethene using halloysite and the only other commercial nucleating for polyethene is rather costly.
Additive to polymer foams
It is common to add mineral particles, such as fine calcium carbonate, or talc, to facilitate the manufacture of polymer foams used for insulation, cushioning and so on. The filler particles provide a surface for the gas bubbles to grown on. This encourages more and finer bubbles, thus engendering a more even (homogeneous) foam with better mechanical properties, insulation performance and lower density. Due to its asymmetrical shape with sharp edges and high surface area, halloysite seemed an excellent candidate for this application.
Extended release of active ingredients
Halloysite tubes are effectively nanocapillary tubes. Capillaries are well known for their ability to suck up liquid, in much the same way a paper towel does. It turns out that the finer the capillary, the more force there is to attract and hold the liquid. The nanosized capillary inside each halloysite tube can be filled with liquid by simply putting the tubes in the liquid and applying mild vacuum to remove the air from inside the tubes. Once inside, the liquid is held there by capillary action. As an example, glycerol, a common humectant in cosmetics, can be released over a period of 24 hours or more to create an all-day moisturizing effect.
Fire retardant for plastics
Halogen free, mineral-based fire retardants for polymers are big business. Popular products include aluminium trihydrate (ATH), magnesium hydroxide (MDH) and huntite/hydromagesite (HMH) described on this page. They operate primarily by liberating water when heated and absorbing heat during their decomposition. Both effects help to quench the flame. Halloysite does release some water, although much less than the other minerals mentioned. Halloysite is also a char former because the surface is catalytic causing the polymer to cross-link and char. Although initially considered a promising use for halloysite, it has not proven commercially attractive and interest has dwindled.
Catalysis
Halloysite was sold in the thousands of tons per year amounts as a cracking catalyst, until it was superseded by newer technology. Clearly then, it has a catalytically active surface. This turns out to be a major problem in polymer applications leading to discoloration (yellowing) and even degradation of the polymer. The problem is the extreme acidity of the mineral surface which may seem odd because the pH in water is almost neutral. Although not widely known, it turns out that as the surface of kaolin is dried, the acidity of the surface sites increases to reach levels equivalent to 90% concentrated sulfuric acid. Although the results published are for kaolinite, halloysite has the same chemistry but higher surface area, further exacerbating the problem.
Commercial aspects
The applications where halloysite has proven to be commercially viable, are ones where the addition level is very low, i.e. 1 weight % or so, or the application itself is niche. So, although halloysite is rare compared to commodity minerals, to date there has been more than sufficient supply to meet demand. Pricing is an important topic.
Conclusion
Halloysite is an unusual and rare natural nanotubular material. Although it does have interesting and unusual properties, new applications in polymers and coatings have been low volume and easily satisfied by existing supply capabilities. So far, the larger potential applications have been thwarted by degradation of the polymer or failure to outperform other incumbent alternatives.
So, now you have an introduction to hallosite filler for plastics, paints, adhesives and more. If you want to dive in and learn even more, then download the Halloysite Handbook which I wrote to help people understand halloysite properties and applications. It contains hundreds of references to peer-reviewed science spanning plastics, adhesives, coatings, catalysis and modification of halloysite surface properties.