PVC Warping in Sunlight
Problem
A large company manufacturing automotive parts contacted me with a very urgent problem. One of their PVC products was warping when exposed to strong sunlight. Prior production runs had shown no issues but the recent lot had serious problems and were failing in the field. The company had their good reputation to uphold and needed a solution quickly.
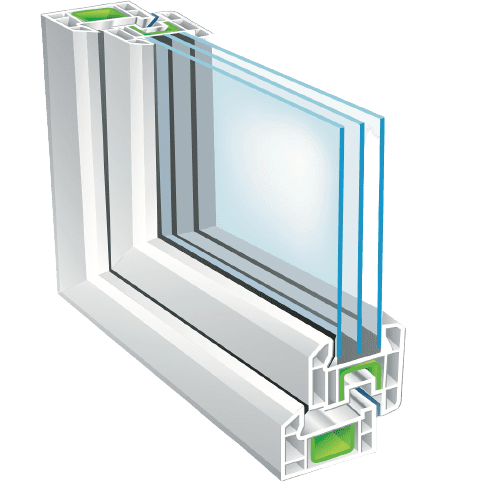
Action
I dropped what I was doing and asked them to overnight me samples of the good lots and the bad lot of extruded PVC parts. I expedited an order for test equipment so I could get to work analyzing the problem as soon as the samples arrived the next day. The next morning I did some measurements in my home lab. It was revealed that the bad lot had a different, softer PVC formulation. My client’s supplier had changed the material formulation without permission. There was also issues with poor compounding whereby the material had variations between one area of the part and the others.
Solution
Based on the measurements, we knew that the compounder could not be trusted, so we moved the business to another compounder. In order to assure there were no more bad lots reaching customers, I provided two simple and quick QC tests that could be performed on every new batch before it was sent out. My client was delighted and their customer was convinced by our fast action plus the new QC tests.
As an added bonus, I found a way to salvage the parts already made from the bad lot of material. Via a simple fix we showed that the warping issues could be avoided, so it was possible to sell the parts instead of scrapping them. My customer was very grateful for this added bonus and continued to come to me with new projects.