Stabilization of Polypropylene (PP)
Problem
This case study about stabilization of polypropylene comes from my time as plastic materials expert at Electrolux, the world’s largest manufacturer of household appliances such as washing machines, dishwashers, refrigerators and so on. I was working at the HQ in Stockholm and taking a coffee break with friends. While chatting, one colleague from another group in R&D mentioned at exciting project he was working on. They had made a condenser out of plastic instead of the normal aluminium. The cool air would run through the channels and the hot water droplets would condense on the outer surface.
The idea had worked much better than expected and was nearing the end of the Stage-Gate process where R&D would hand it over to production. I told him how impressed I was and remarked “wow, with a PP plastic sheet that’s so thin combined with hot water exposure, you must have used an incredibly effective set of antioxidants/stabilizers to make that durable enough to work.” He replied “what’s a stabilizer?” And that’s when I knew we had an emergency on our hands – without action, the product was certain to fail, leading to a recall and damaged reputation.
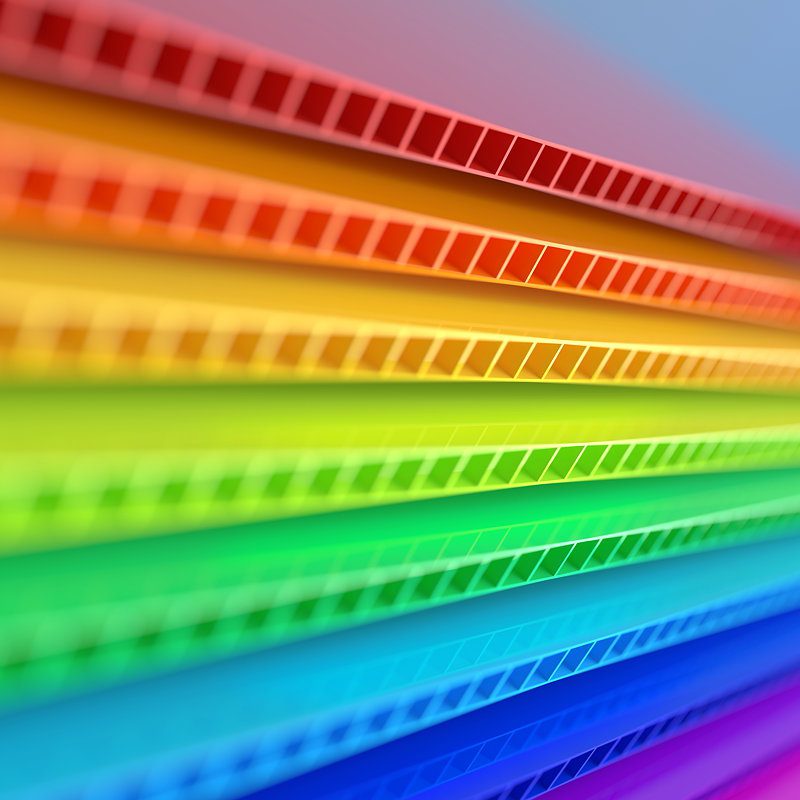
Action
While the general public view plastics as stable materials, plastics scientists know that the exact opposite is the case. Polypropylene (PP) is one of the most common thermoplastics and yet it is unusable in the virgin, unmodified state because the instant that PP is created, it comes under attack by oxygen in the air and begins to degrade. It’s almost like watching an apple as it goes brown and oxidizes, in fact the chemistry is similar. It has been shown that a PP film left at room temperature in the dark loses all strength and crumbles in less that a year. By contrast, a piece of paper takes over 2000 years to degrade under the same conditions.
PP is only usable when antioxidants are added as stabilizers to slow down the oxidation chemistry which is a chain reaction. In most cases, a very low concentration of antioxidant is used because it costs money and they want to use the minimum amount. The material my colleague had used was not usually used in extreme conditions, so I suspected that it would not be anywhere near durable enough to survive with hot water condensing on it. To test that, we immediately performed an accelerated test called oven ageing. We put a piece of the plastic in an over at 150°C. A highly stabilized piece of PP would survive for months at that temperature. How long did this piece of polypropylene survive in the oven? It had gone yellow and crumbled into pieces overnight! It had only enough stabilizer for weeks or months in service, not the decades required for that appliance.
Solution
In order to save the situation, we needed to design an extremely effective, state of the art, additive package for the stabilization of polypropylene. Not only that but we would need a rapid, accelerated test to verify that the additives were effective enough. Because PP is so very unstable, we were not certain that even the best stabilization package could protect it for this new application. Hot conditions accelerate oxidative degradation and water washes the stabilizers out of the plastic, leaving it unprotected.
First, we took several steps to dramatically increase the effectiveness of the stabilization package:
- We abandoned the normal stabilizers like Irganox 1076 and 1010
- We moved to more hydrophobic stabilizers that resist extraction by water
- We moved to stabilizers that are chemically able to withstand hot water (1076 and 1010 hydrolyze and fall to pieces)
- We moved to stabilizers with much higher molecular weight because larger molecules stay in the plastic much longer
- We used a synergistic mixture of stabilizers with different chemistries
- We avoided certain stabilizers known to have an antagonistic effect
- We massively increased the total stabilizer concentration
Next we designed a new accelerated test. The usual test for household appliances is oven ageing but that does not mimic the hot water exposure that was needed in this instance. Our new test exposed the material to boiling, condensing water 24/7, so that we could simulate many years of ageing in just a few weeks. We were relieved and surprised that the material passed with flying colors. No discoloration or degradation was found.
Phantom has deep expertise when it comes to stabilization of polypropylene, polyethylene and other plastic materials including nylon 12 used in 3D SLS printing, other nylons, polyesters and styrenic polymers like SBS, ABS and ASA. Another case we worked on was a class action case involving Marlex medical mesh used for hernia and vaginal repair. The Marlex mesh is made of polypropylene but was found not to have proper stabilization for use in the body. The elevated temperature combined with water exposure, which extracts the antioxidant from the very thin mesh fibers, creates a challenge. The mesh investigated was found to have neither the correct type nor amount of stabilizers. Read more about the Marlex mesh case study here. Learn more about corrugated polypropylene sheet here.
Many case studies of problems solved can be found in the dropdown menu on the homepage. Even if you don’t see your exact problem listed there, give Phantom a call anyway and I’ll tell you whether I can help.
Improving synthetic hindered phenol antioxidants; Learning a lesson from vitamin E K. D. Breese, J.-F. Lamèthe and C. DeArmitt, Polymer Degradation and Stability, 70, 89, (2000).
Synthesis and evaluation of hyperbranched phenolic antioxidants of three different generations H. Bergenudd, P. Eriksson, C. DeArmitt, B. Stenberg, E. Malmström Jonsson, 76, 503-509, (2002).